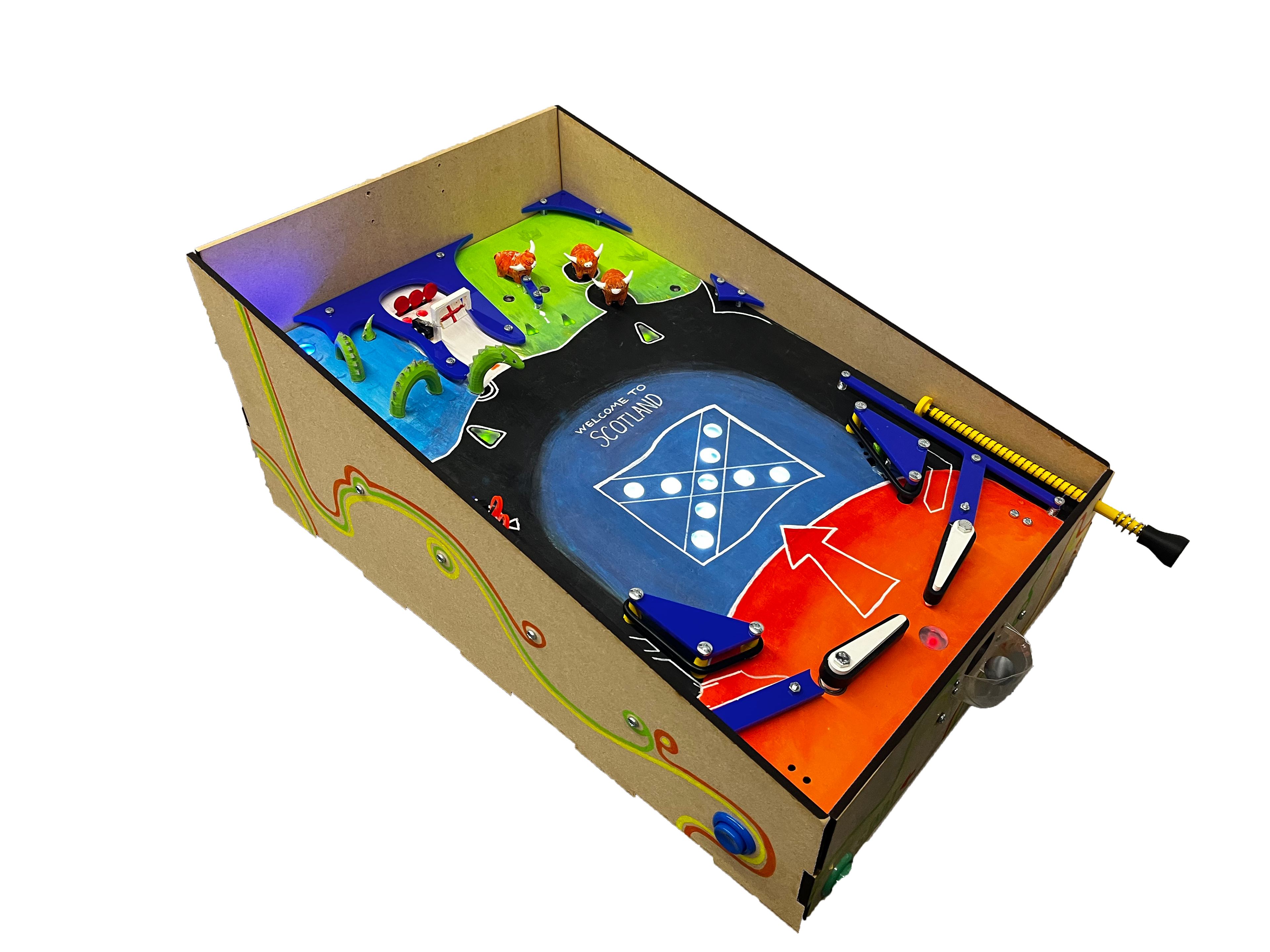
For the Olin course Principles of Integrated Engineering, I modeled and built a pinball machine alongside three other people. Using Onshape, I modeled four mechanical components of the pinball machine: the slingshot, the spinner, and the stand-ups. Slingshots are next to the flippers. They are triangles with rubber tubing wrapped around them with tension. When the ball hits a slingshot, a lever pushes on the rubber tubing and “slings” the ball across the playfield. The spinner is a piece of plastic that, when hit by the ball, will spin, causing a wire to flip a microswitch, giving the player points. Stand-ups are levers from which the ball can hit and gain points.
For this project, my team and I were limited to using 3D printers and laser cutters. This challenge proved difficult to overcome; however, after rapid prototyping and co-designing, the product came out just as I had wanted it to. There was a difficult balance of creating a 3D print that would fit into the box but also be sturdy enough to withstand the forces of the electrical components, such as the solenoids, without breaking. This can be seen in the slingshot diagram below. I fabricated the hardboard housing for the electronics using laser cutters, and all of the mechanical components were fabricated using 3D-printed PLA plastic and laser-cut acrylic.
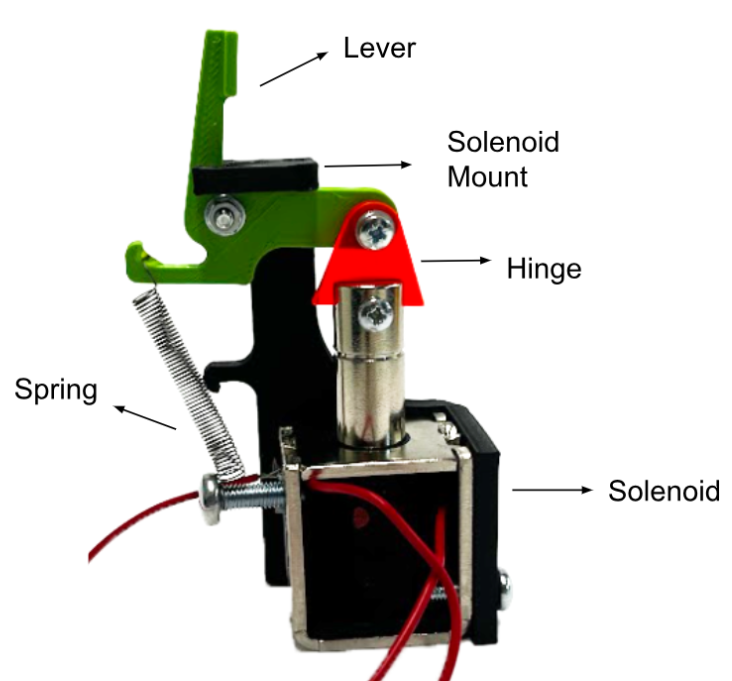
Slingshot Mechanism
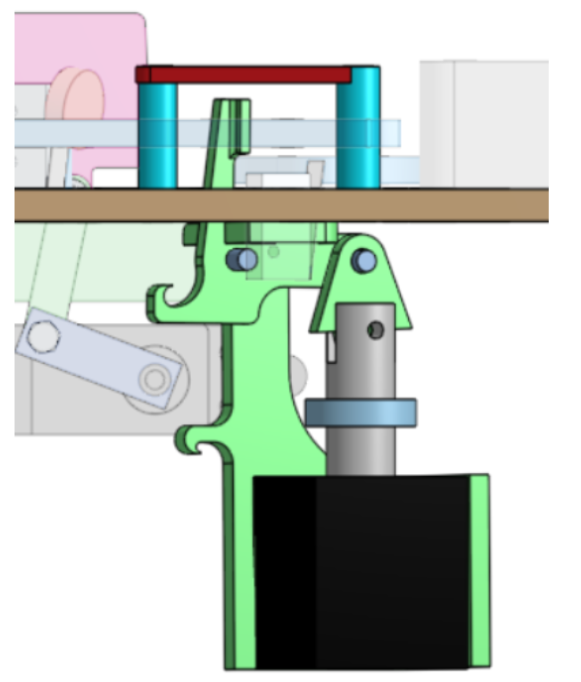
Slingshot CAD
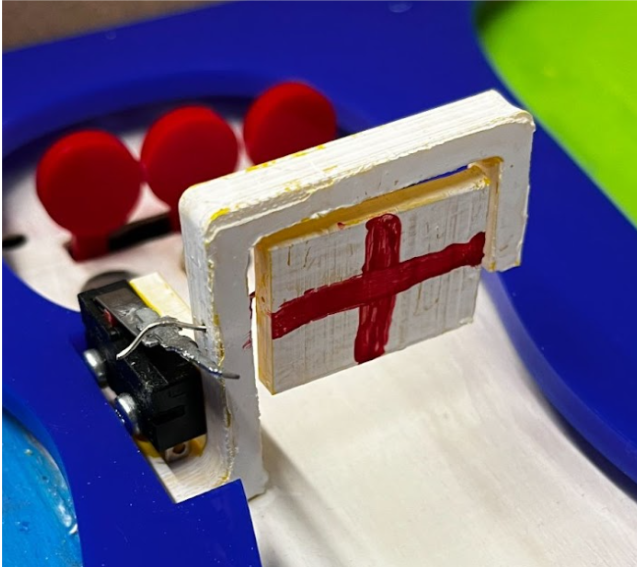
Spinner
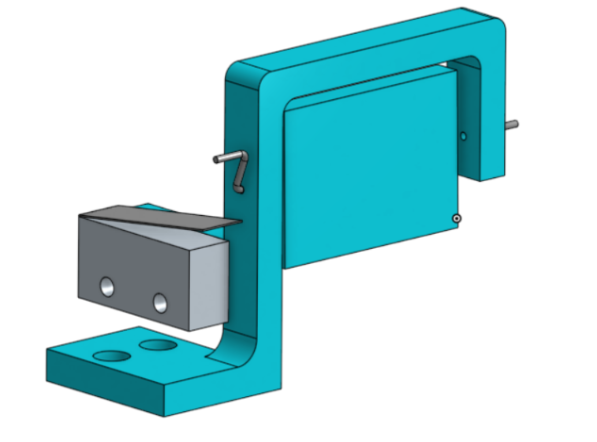
Spinner CAD
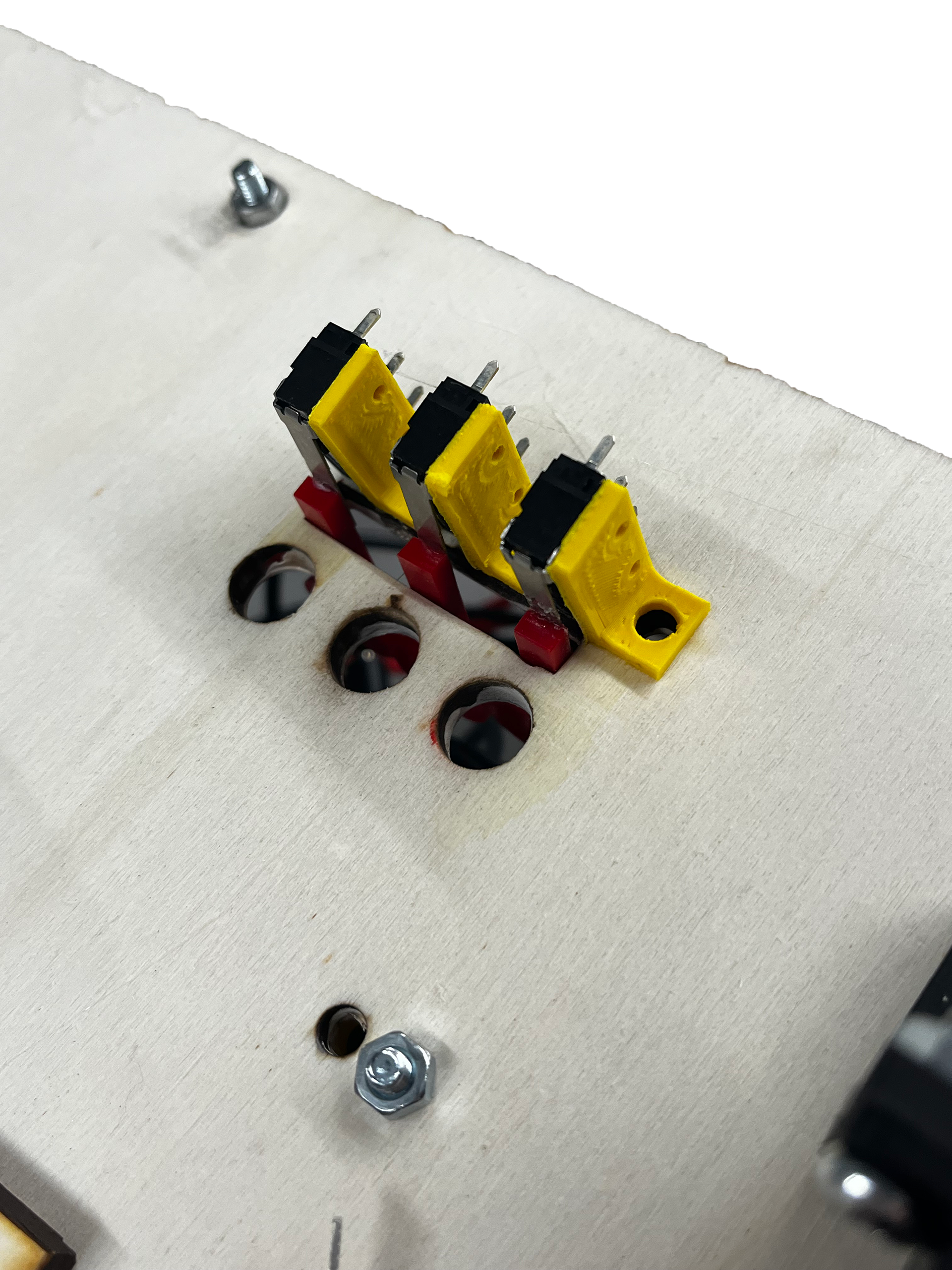
Stand-Up Mechanism
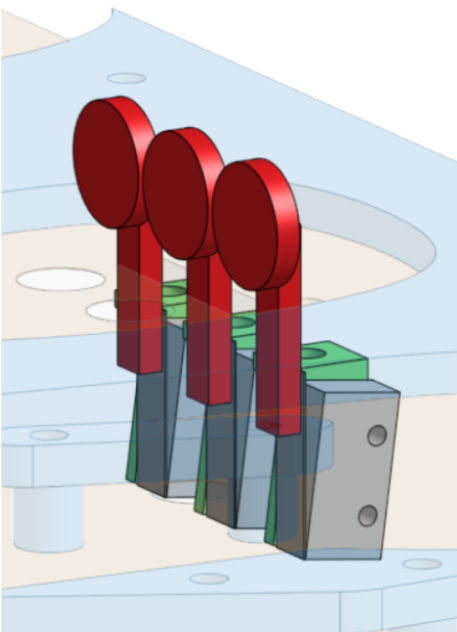
Stand-Up CAD
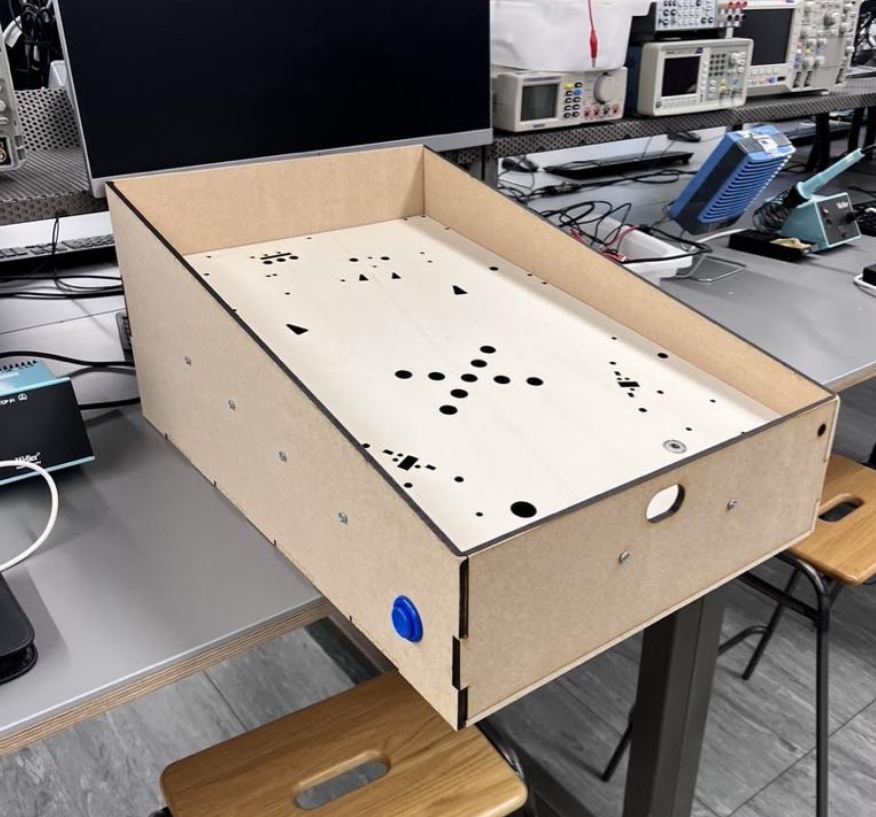
Hardboard Housing